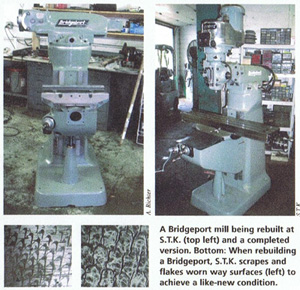
"The machine costs $15,000 to purchase new and we can rebuild it for 40 to 50 percent of that price," said Colon Kelly, the company's sales manager.
"Bridgeport mills last because they made these machines so well," he added. "The castings are second to none, and that's the difference between a Bridgeport mill and an older machine that doesn't last."
The company offers two rebuilding options. The first is a partial rebuild for $4,100, wherein BMR repairs the head as needed and any additional cost for repairing the head will not exceed the complete rebuild cost. The second option is a complete rebuild, which takes 2 to 3 weeks, runs $6,100 and includes some 18 procedures. Either way, the customer receives a milling machine that performs as well as the original.
"There's no difference (between a new and rebuilt machine) as long as we're not remanufacturing or retrofitting a CNC to the machine," Kelly said.
The process of remanufacturing is basically rebuilding the machine back to its original specifications and then the remanufacturing part is just filling in the gap to take the machine to current levels of technology. "When you start remanufacturing," he said, "you get closer to a new product's cost and you may as well buy a new machine."
In addition to rebuilding a machine a customer ships and delivering it when the work is completed, BMR often can sell an already rebuilt machine so the loss of production capacity is minimized. "A lot of times, customers contact us first to see if we have a machine comparable to what they use," Kelly noted. If so, BMR will ship the comparable machine, rebuild the one the customer sends and "then the process starts where they'll send us a machine and we'll send them one. It goes back and forth."
The rebuilder maintains an inventory of six or seven Bridgeport mills that it intends to rebuild, but is selective about the used machines it purchases because of limited storage space. "We're a rebuilder. We want to buy machines that really need to be worked on," Kelly said.
Bridgeport Machine Rebuilders isn't limited to rebuilding Bridgeport mills. The company also rebuilds other equipment, such as Mitsui and Harig surface grinders. Recently, the company has branched out into rebuilding CNC machines, which takes around 10 weeks. Recently, BMR was rebuilding two Mazak VQC-15/40 CNC machines. "That is the future," Kelly said. "We're not going to get away from rebuilding the Bridgeports and the Mitsuis, but we're also going to venture into the CNCs some more." In addition to rebuilding the machines, BMR is adding a 3-D simulation software package.
With the manufacturing economy doing well and the company targeting additional types of rebuilding work, Bridgeport Machine Rebuilders finds itself in the enviable position of having a backlog. "We have enough work now to last the rest of the year," Kelly said in August.
- A. Richter